Sydney Airport A380 Airfield Works
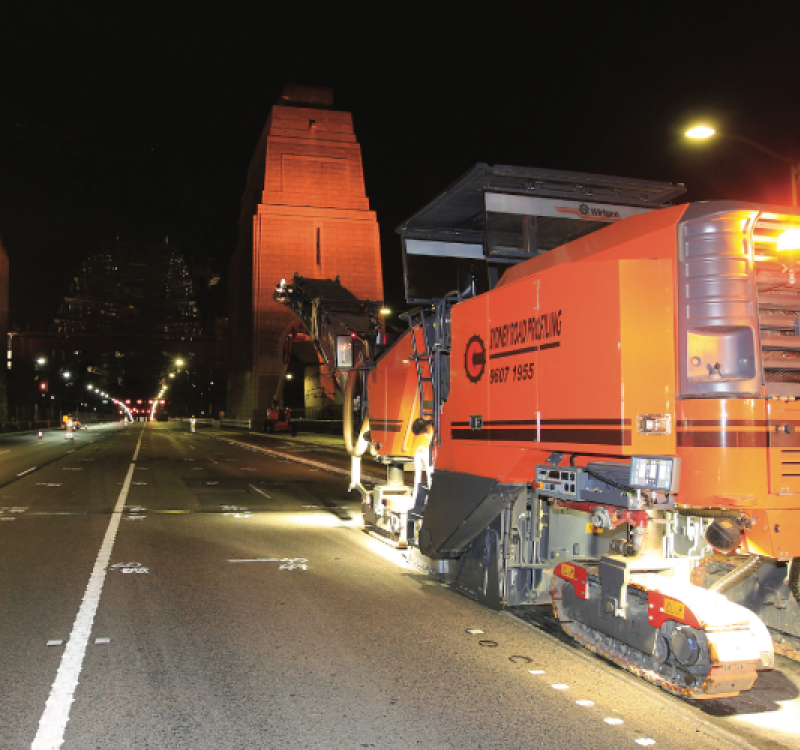
The Project
Commissioned by Road and Maritime Services (RMS) alongside several other contractors, SRP and The Kypreos Group were allowed two weekends and another for contingency to complete the milling, with approximately 8-10 hours per weekend.
Without needing the back-up weekend, The Kypreos Group wrapped up the operation within the allotted time, with stellar outcome. Surveying of the milling job after it was done showed that all levels were within a minute ± 5mm. This profiling ensured a clean, flat base for the new waterproofing membrane and the new and smoother asphalt driving surface for travelling vehicles.
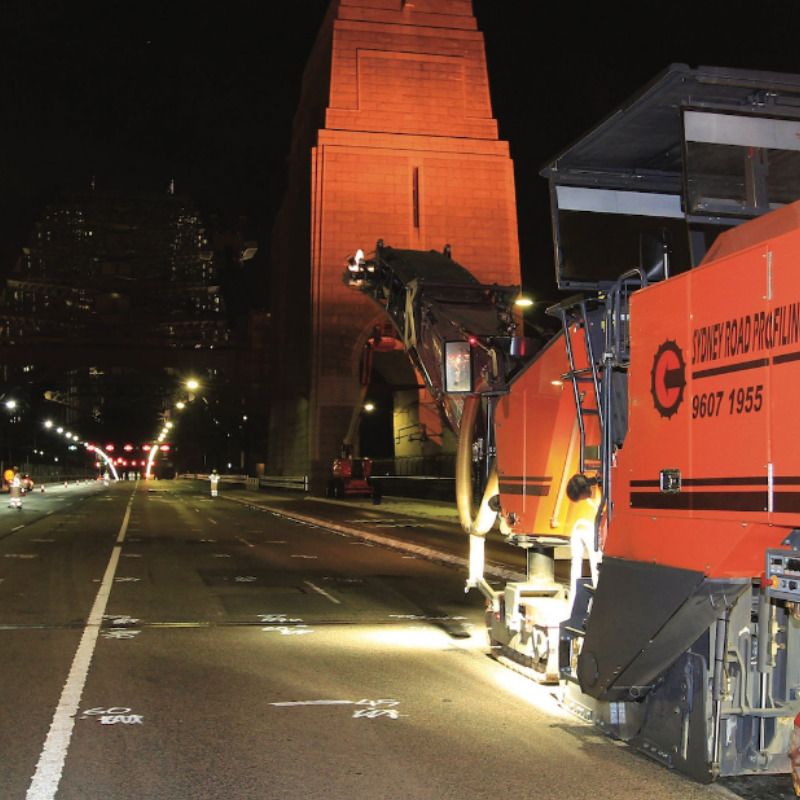
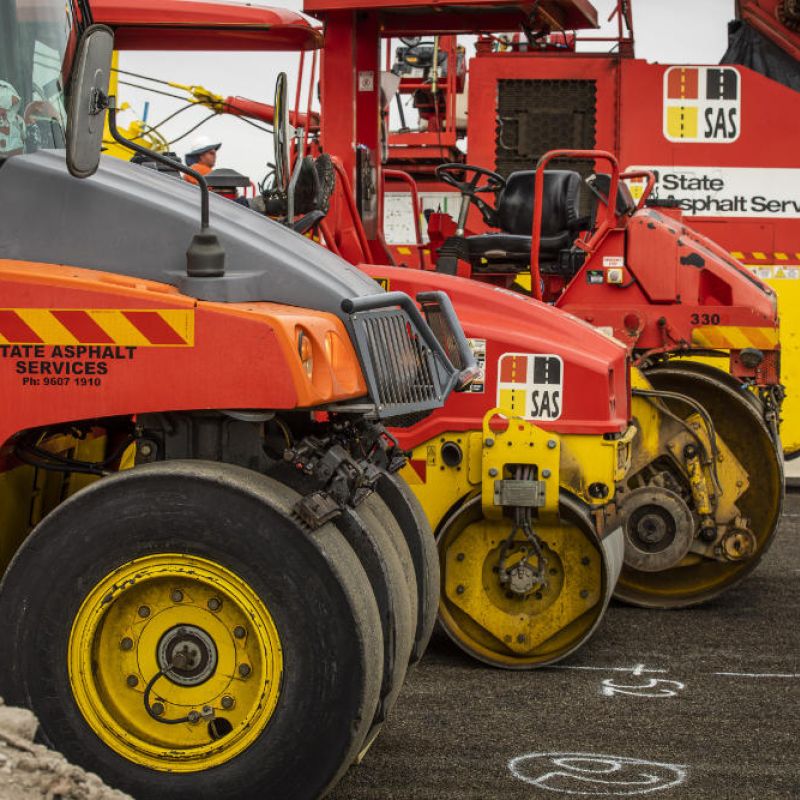
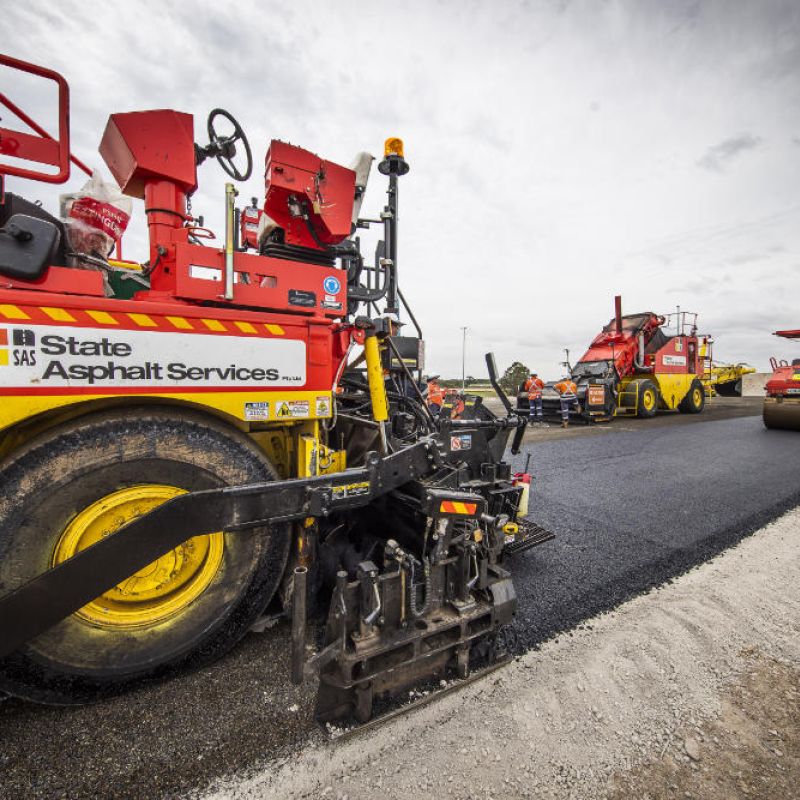
Client
Roads and Maritime Services (RMS)
Estimated Cost
$3M
Completion Date
March 19, 2012
Location
Sydney
Description
On 19th March 2012, the iconic Sydney Harbour Bridge celebrated its 80th birthday. This monumental occasion called for complete re-profiling of the deck to improve the waterproofing and asphalt surfacing, reducing the need for later reactive maintenance. Except for small-scale trials prior to its start, the project was the first ever of its kind since the Bridge’s construction decades ago.
Sydney Road Profiling (SRP) – part of The Kypreos Group – took on the entire milling works. From organisation and management to execution of this mammoth part of the operation, we delivered.
Client Challenge
The most challenging aspect of the Harbour Bridge re-profiling project was the sheer amount of logistics that went into it, all having to comply with the time allowance. The status of Harbour Bridge as one of Australia’s largest iconic structures and key transport gateways gave the project high publicity, adding to the already immense pressure. This was a road that had to be opened on time, no matter what, so there was no room for error.
Assembling all the pieces of plant and trucks was a tough task given the central location of the job site. All approaching roads had to be closed off with the help of police escorts. This massive number of workers and equipment, all in a restricted site rushing against time pressure, raised the risk of injury significantly which required immense care and thorough planning to minimise.
Also, there was the critical need to moderate the amount of water used to curb the dust produced during milling, since a too-wet milled surface would hinder the subsequent application of the waterproofing membrane.
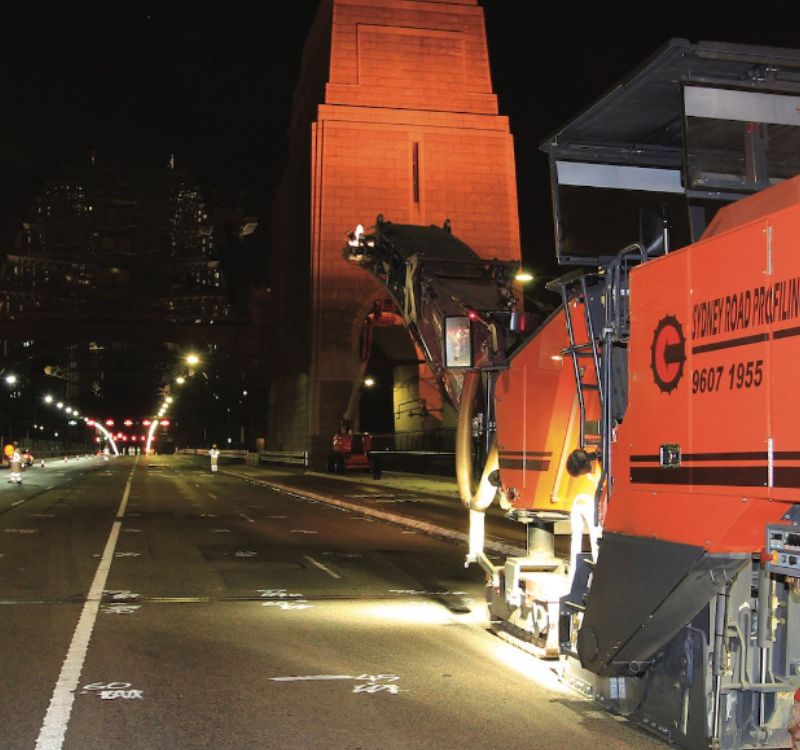
What We Delivered
By committing to taking on the responsibility of organising the entire milling works, SRP and The Kypreos Group stood out. Few other profiling companies would want to manage a project of this size from start to finish like requested by RMS: most organisations would prefer simply hiring out their machines and operators and leaving the management to another party.
This thorough commitment involved fortnightly planning meetings with RMS to discuss, in painstaking detail, options to tackle the project and to solve any restrictions as they cropped up. It also entailed hiring and managing additional external labouring crews and profilers, trucks, jackhammers and bobcats.
The Kypreos Group brought our entire fleet of profilers to this operation: Wirtgen W210, Wirtgen W2000, Wirtgen W100F, Wirtgen W350, Caterpillar PM-200, Caterpillar 226B, Bobcat S250 plus various trucks and air compressors. On the second night, there were over 75 pieces of plants and more than 120 people all managed by us, of that 8 pieces of plants and 18 workers were in-house.
All the operators were handpicked for the project and needed to be able to work quickly and, most importantly, accurately while under immense pressure, and the machines must be in perfect working order. SRP and The Kypreos Group had unique stickers made for all the trucks and plant so they were easily identified and contactable, the plant movements were planned out to the metre. Everything was timed and organised to the quarter hour. The success of the project was down to such detail and strict safety management.